امروزه بسیاری از سازمان ها در تلاشند تا سیستم های ناب را با سیستم های از رده خارج شده تولید انبوه خود جایگزین نمایند تا از این طریق، کیفیت محصولات خود را افزایش داده، اتلاف ها را حذف نموده و تاخیرها و هزینه کل را نیز به حداقل برسانند.
سیستم های ناب بر جلوگیری از وقوع اتلاف ها و هرگونه افزایش در زمان، نیروی انسانی ،مواد مصرفی تولید و یا خدمات که ارزش افزوده ای ایجاد نمی کنند تاکید دارند. ابزارها، تکنیک ها و روش های ارائه شده در سیستم ناب می تواند سازمان را در دستیابی به اهداف کاهش هزینه، تحویل بهنگام و کاهش زمان سفارش تا تحویل یاری رسانند. در یک سازمان ناب، فرهنگ بهبود مداوم در کلیه سطوح شغلی و فرایندهای موسسه گسترش می یابد.
همچنین از آنجاییکه تمرکز این نوع سیستم ها بر نیازمندی های مشتریان می باشد، خدمات و تولیدات حاصله را به میزان مناسب، در بهترین زمان و مکان و با مطلوبترین شرایط در اختیار مصرف کننده قرار می دهند. کالاها و خدمات بر اساس سفارش یک مشتری خاص تولید می شوند نه با هدف پر کردن انبارهای سازمان. در یک سازمان ناب می توان طیف گسترده ای از کالاها و خدمات با کیفیت را تولید نمود و در عین حال نوسانات تقاضا در بازار را به خوبی پوشش داد.
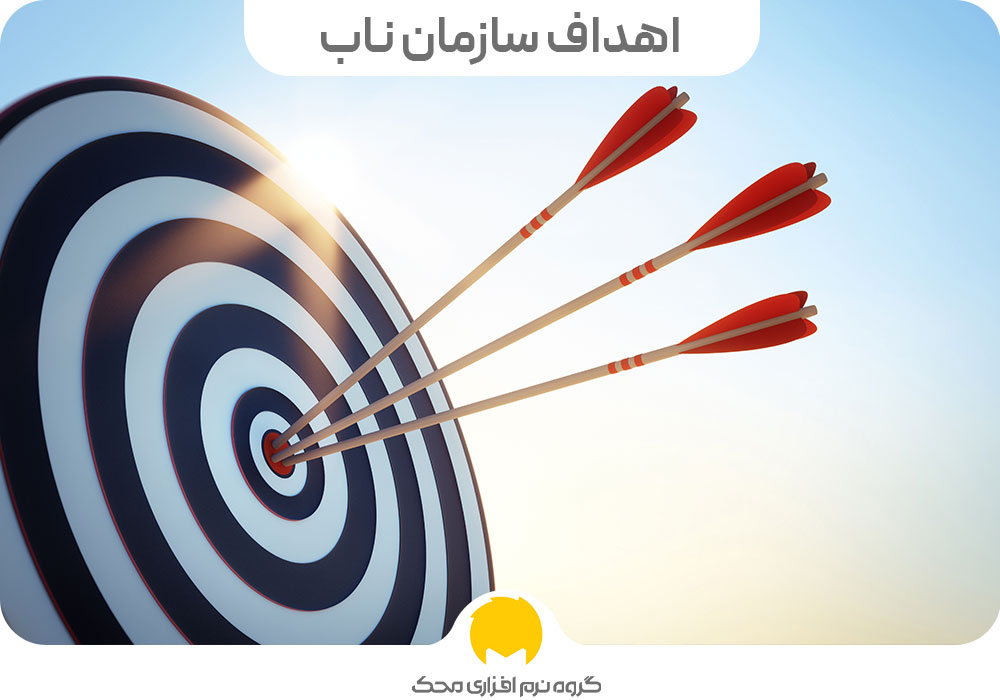
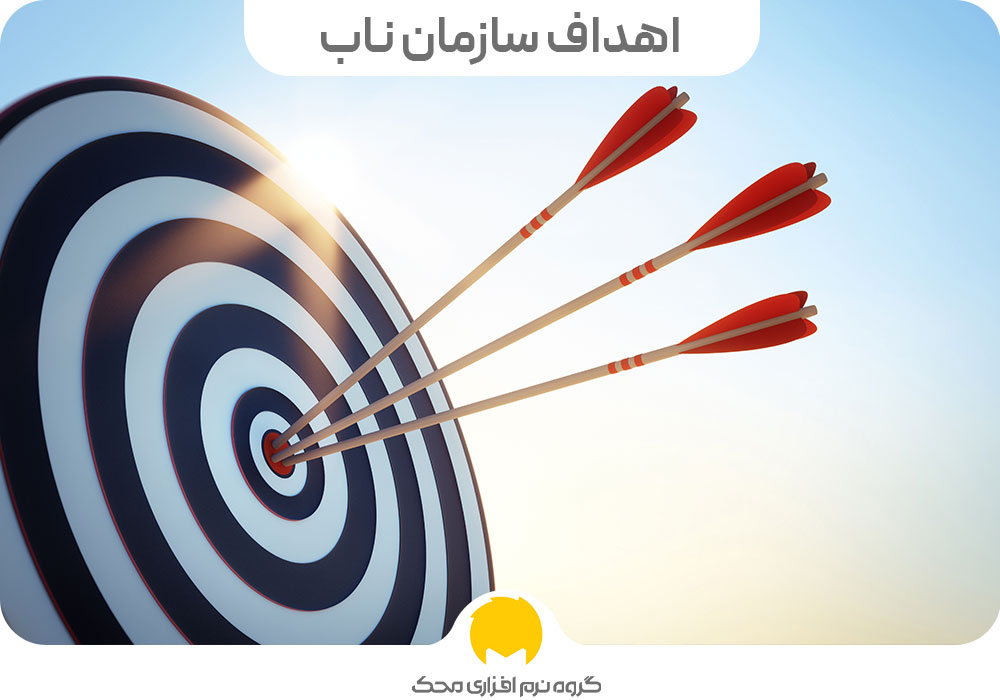
اهداف سازمان ناب
می توان از متدها و تکنیک های ناب در راستای ارائه ارزش های بیشتر به مشتریان سازمان بهره مند شد. بدین ترتیب قادر خواهید بود به 4 هدف اساسی زیر دست یابید:
هدف اول: بهبود کیفیت
منظور از کیفیت، توانایی برآورده ساختن نیازهای مشتریان از طریق ارائه کالاها و خدمات تولیدی می باشد. این نیازمندی ها انتظارات و خواسته های اعلام شده و اعلام نشده مشتریان را شامل می شود. کیفیت کالا ها و خدمات اولین قدم سازمان برای بقا در بازارهای رقابتی است.
چگونه می توان کیفیت را افزایش داد ؟
- فرآیند بهبود کیفیت را از درک نیازمندی ها و خواسته های مشتریان آغاز نمائید.
- ابزارهایی مانند ” گسترش وظایف کیفی ” می توانند کمک موثری برای درک این نیازمندی ها ارائه دهند.
- مشخصه های طراحی کالاها و خدمات را مرور نمایید تا از توانایی پاسخ گویی به انتظارات مشتریان مطمئن شوید.
- فرآیندها و شاخص های اندازه گیری هر فرآیند را بررسی کنید تا از قابلیت آنها برای کسب رضایت مشتری اطمینان حاصل نمائید.
- محدوده هایی را که باعث به وجود آمدن عیوب در کالاها و خدمات می گردند شناسائی نمائید.
- از روش های حل مساله برای تعیین علل ریشه ای مشکلات استفاده کنید.
- تکنیک های حل مساله را برای جلوگیری از بروز ایرادات احتمالی در فرآیند به کار ببرید. ممکن است در شرایطی مجبور به تغییر در محصول، خدمت و یا فرآیندهای مرتبط باشید.
- از شاخص های عملکرد به منظور ارزیابی اثربخشی راه حل ها استفاده نمایید.
هدف دوم : حذف اتلاف ها
اتلاف به عملیاتی گفته می شود که طی آن زمان یا سایر منابع به کار گرفته شده اما هیچ ارزش افزوده ای برای کالا یا خدمت ایجاد نمی نماید. ارزش افزوده هنگامی رخ می دهد که دگرگونی انجام شود، مواد خام تغییر شکل پیدا کرده و یا اطلاعات نیازمندی های مشتریان اخذ گردد. برخی فعالیت ها از قبیل حمل و نقل مواد در حین فرآیند تولید محصول، ممکن است ضروری باشد اما ارزش افزوده ای ایجاد نمی نمایند. یکی از اولین اهداف سازمان ناب، ارائه کالا و خدمت با کیفیت به مشتری می باشد. در یک سازمان ناب این اهداف با حذف تمام اتلاف ها و توجه به مراکزی که ارزش افزوده ایجاد نمی کنند، ولی برای تولید ضروری است حاصل می شود.
به منظور شناسایی و حذف اتلاف ها، فرایندی را در نظر بگیرید که به بهترین نحوه در شرایط زیر فعالیت می کند:
- محصولات و یا خدمات تنها براساس سفارش تولید می شوند و نه با هدف ذخیره کردن در انبارها.
- سازمان در تلاش است تا به نیازمندی های مشتریان سریعا پاسخ داده شود.
- حجم ضایعات و ذخیره محصولات و مواد مصرفی در انبارها صفر باشد.
- تحویل محصولات و خدمات به مشتری بسیار سریع و آنی باشد.
با تصور اجرای چنین عملیاتی، متوجه خواهید شد که چقدر اتلاف در سازمان شما مخفی شده است. استفاده از چنین روش هایی شما را قادر می سازد تا اتلاف ها را از بین برده و به سطح مطلوب اجرای عملیات نزدیکتر شوید.
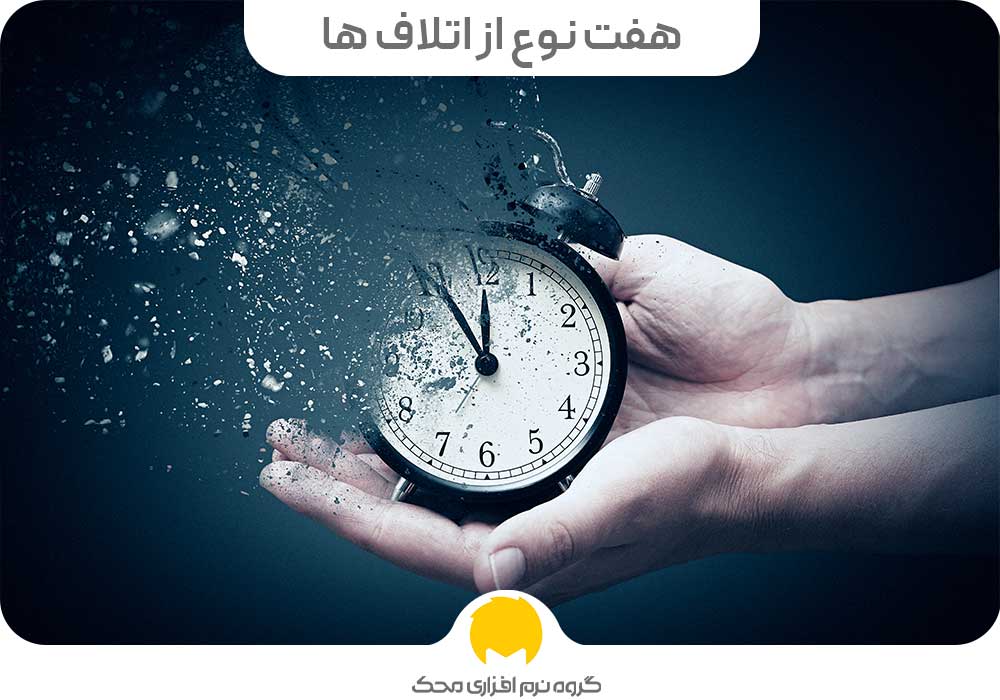
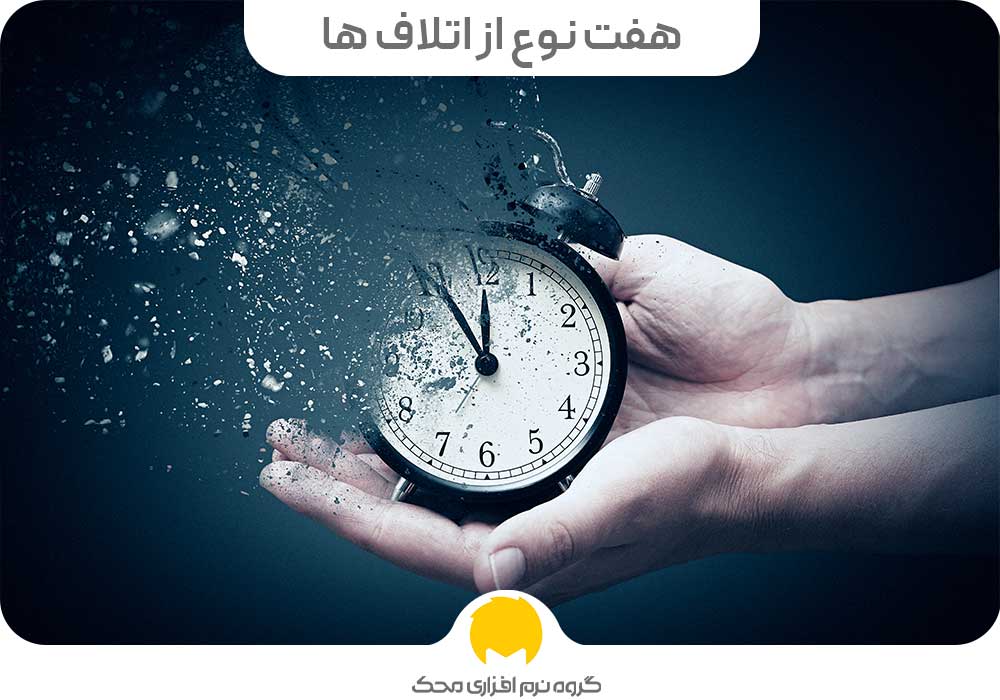
هفت نوع از اتلاف ها
هنگام استفاده از ابزارها و تکنیک های تولید ناب بایستی تدابیری اندیشید تا 7 نوع اتلافی که در ادامه توضیح داده می شود نیز حذف گردند:
1- تولید مازاد: بدترین نوع اتلاف، تولید بیش از حد نیاز است. یعنی ادامه تولید در زمانی که مشتری برای محصول تولیدی وجود نداشته باشد. نتایج حاصل از این امر عبارتند از 1.وجود تولید مازاد در شرکت 2.تولید محصول بدون در نظر گرفتن نیازمندی های مشتری
2- انتظار: که به معنی صف بندی نیز می باشد. این شرایطی است در زمانی اتفاق می افتد که فعالیت ایستگاه های اولیه به موقع انجام نشده و به همین دلیل افرادی که در ایستگاه های بعدی هستند بیکار می مانند. در چنین حالتی پرسنل ایستگاه کاری بعدی یا مجبور به انجام کارهایی می شوند که ارزش افزوده ای ایجاد نمی کنند یا بدتر از آن این که کارهایی انجام می دهند که منجر به تولید مازاد شود.
3- حمل و نقل: این آیتم شامل نقل و انتقال غیرضروری مواد می شود مانند انتقال موجودی حین فرآیند از یک ایستگاه به ایستگاه دیگر . به 2 دلیل بایستی حمل و نقل را به حداقل رساند. 1- این عمل زمان فرایند را اضافه می کند بدون این که ارزش افزوده ای به وجود آورد. 2- اقلام ممکن است در حین عملیات حمل و نقل آسیب ببینند.
4- فرایند مازاد: این آیتم فعالیت های مازاد مانند دوباره کاری، اجرای مجدد یک فرآیند، حمل و نقل و اقذامات مرتبط با انبارکردن مواد و قطعات را شامل می شود که معمولا به دلیل وجود ایرادات در محصول، تولید مازاد و همچنین حجم بسیار کم و یا زیاد موجودی اتفاق می افتد. مثال دیگر در این زمینه هنگامی است که یکی از پرسنل بخش فروش باید آن دسته اطلاعات مشتری را که بایستی قبلا توسط پرسنل سایر قسمت ها جمع آوری میشده را گردآوری نماید. اثربخشی یک فرآیند هنگامی به حداکثر خواهد رسید که فعالیت در اولین بار به صورت صحیح انجام شود و از انجام دوباره کاری ها و اصلاح ایرادات جلوگیری به عمل آید.
5- موجودی مازاد: این بخش شامل آن دسته از موجودی هاست که به صورت مستقیم برای انجام سفارش جاری مشتری استفاده نمی شوند. این اقلام شامل مواد خام ،موجودی حین فرآیند و کالاهای ساخته شده هستند. انبارکردن موجودی مازاد بدین معناست که سازمان بایستی تا زمان دریافت سفارش خرید برای آن مورد بخصوص محلی را برای ذخیره کردن آن تخصیص دهد. موجودی های مازاد همچنین آن دسته از اقلامی که بایستی برای مشتریان ارسال شوند ولی هنوز ارسال نشده اند و تجهیزات یدکی که هیچگاه مورد استفاده قرار نمی گیرند را هم شامل می شوند.
6- حرکت و جابه جایی: منظور از این آیتم، اجرای فعالیت هایی است که با هدف رفع مشکلاتی از قبیل چیدمان نامناسب، ایرادات محصول تعریف مجدد فرآیندها تولید مازاد و نامتناسب بودن موجودی ها انجام می شود.حرکت و جابه جایی ها نیز مانند حمل و نقل زمانبر بوده و ارزش افزوده ای ایجاد نمی نماید. مثالی که می توان در این خصوص ارائه داد: کارگری است که برای استفاده از ابزارهای مورد نیازش بایستی به دور خود بچرخد و این ابزار و مواد در محل مناسبی قرار ندارند.
7- ایرادات: بدین معنی که محصول و یا بخشی از خدمت ارائه شده به مشتری به نحوی است که قادر به جلب رضایت وی نبوده و لذا مشتری اظهار نارضایتی می نماید. نتایجی که از این ایرادات حاصل می شود. عبارتند از هزینه های پنهان ،عودت محصولات فروش رفته، مشاجرات داخلی سازمان و در نهایت کاهش حجم فروش. فرآیندهای ستادی نیز می توانند با انجام برخی فعالیت ها از قبیل ثبت اطلاعات اشتباه در فرم های جاری با ایرادات مواجه شوند.
چگونه میتوان اتلاف ها را حذف کرد؟
- پس از شناسایی یک محصول و یا عملیات ناکارا تیمی را با هدف کاهش اتلاف ها تشکیل دهید.
- فرآیندهایی که عملکرد ضعیفی داشته و یا نیاز به انجام اقدامات اصلاحی دارند را مشخص نمائید. در صورت اطمینان از انتخاب صحیح ،فعالیت دارای کمترین خروجی را به عنوان نقطه شروع عملیات انتخاب کنید.
- یک نقشه جریان ارزش برای فعالیتی که تحت بررسی است تهیه نمایید.
- نقشه جریان ارزش را مرور کنید تا محدوده، حجم و میزان تکرار هفت نوع اتلاف داده شده برای فعالیت مورد نظر را تعیین نمائید.
- شاخص هائی را برای تعیین حجم و میزان تکرار مجموعه اتلاف های این فعالیت تعریف نمائید.
- گام های حل مساله را با استفاده از اصول ناب و به منظور کاهش و یا حذف اتلاف ها آغاز نمائید.
- به منظور حصول اطمینان از روند کاهش اتلاف ها شاخص های تعیین شده را به صورت دوره ای مرور کنید.
- این فرآیند برای سایر فعالیت هائی که بهره وری پایینی دارند تکرار شود.
هدف سوم : کاهش زمان سفارش یا تحویل
زمان سفارش یا تحویل مجموعه زمان های صرف شده برای تکمیل یک سری از وظایف در حین فرآیند است. به عنوان مثال فاصله زمانی بین ارسال یک سفارش برای مشتریان و دریافت وجه آن و یا فاصله زمانی مورد نیاز برای تبدیل مواد خام به کالای ساخته شده و همچنین فاصله زمانی معرفی محصول جدید پس از اتمام مرحله طراحی.
یک سازمان ناب میتواند از طریق کاهش زمان سفارش تا تحویل، سریعا به تغییر در تقاضای مشتریان پاسخ گفته و نرخ بازگشت سرمایه خود را بهبود ببخشد. زمان های سیکل فرآیند می تواند به 3 جزء اصلی تقسیم شوند که عبارتند از:
- زمان سیکل اجرا: به زمانی گفته می شود که برای تکمیل یک فرآیند کاری مانند تولید یک قطعه و یا تکمیل یک سفارش فروش مورد نیاز است.
- تاخیر گروهی: مدت زمانی است که یک فعالیت یا محصول بایستی در انتظار بماند تا سایر فعالیت ها و یا قطعات ایجاد شوند. به طور مثال مدت زمانی که یک قطعه ماشین کاری شده بایستی متوقف شود تا قطعه بعدی هم عملیات ماشین کاری را پشت سر گذارده و به صورت بچ درآیند و یا مدت زمانی که یک سفارش آماده شده و منتظر تکمیل سفارش بعدی است تا به اتفاق ارسال گردند.
- تاخیر فرآیند: مدت زمانی است که هر بچ تکمیل شده در انتظار می ماند تا فعالیت بعدی آغاز شود. به طور مثال مدت زمانی که یک مجموعه قطعات ماشین کاری شده باید در انبار بمانند تا فعالیت بعدی شروع شود و یا یک سفارش ثبت شده و مشتری باید معطل شود تا تائیدیه ارسال آن از مدیریت مربوطه اخذ گردد.
همزمان با بررسی روش هایی که می تواند زمان سفارش تا تحویل را برای تولید محصول و یا ارائه خدمات کاهش دهد، فرآیندهای زیر را هم به عنوان محدوده های بهبود در نظر داشته باشید.
- طراحی مهندسی
- اخذ سفارش
- برنامه ریزی تولید
- خرید
- انجام سفارش
- دریافت
- تولید
- بازرسی / دوباره کاری
- بسته بندی
- حمل و نقل
- جمع آوری فاکتورها و پرداخت ها
در زیر لیستی از راه حل های محتمل برای کاهش زمان سفارش تا تحویل و اهداف هر راه حل ارائه شده است. این راه حل ها به 3 گروه تقسیم شده اند که عبارتند از : طراحی محصول، ساخت و تامین
طراحی محصول
توجیه عقلی محصول در این مرحله خصیصه ها و متغیرهای یک محصول یا خدمت با هدف دستیابی مستقیم به نیازمندی و خواسته های مشتری تعیین می گردد.
ساخت
شبیه سازی فرآیند: این امکان به شما کمک می کند تا فرآیند مورد نظرتان را به صورت یک مدل درآورید و از این طریق اتلاف ها آشکار شده و میزان اثربخشی راه حل های پیشنهادی مشخص می گردد.
تاخیر با هدف تطابق محصول با نیاز مشتری: یعنی انتظار تا زمان اتمام سیکل تولید به منظور شکل دهی یا تغییر محصول مطابق با سلیقه مشتری
جریان مداوم یا تکی محصولات و اطلاعات: در این حالت قادر خواهید بود تاخیرات فرآیند و بچ های تولیدی را حذف نمایید.
راه حل های تکنولوژیکی نرم افزاری و سخت افزاری: به منظور کسب توانائی در خصوص کاهش و یا حذف اشتباهات
تعویض سریع: در این حالت اندازه هر بچ محصول یا خدمت تا حد ممکن کوچک شده و بنابراین قادر خواهد بود به سفارشات مشتری سریع تر پاسخ دهید.
استاندارد سازی فرآیند: به معنای شناسائی منبع پیدایش اتلاف ها و سپس استانداردسازی بهترین روش اجرای عملیات با هدف حذف آنهاست.
تامین
با انجام تحلیل تقاضا، زنجیره تامین می توانید اتلاف های مرتبط با لجستیک را شناسائی نمائید. در این حالت موجودی مازاد ناشی از طولانی بودن زمان انتظار که موجب تولید بیش از حد نیاز می شود مشخص میگردد. تحلیل های بخش حمل و نقل مشخص می کند که گاهی اوقات تولید بیش از حد نیاز به دلیل استفاده از تخفیف های حمل است. اما این تخفیف ها ضرورتا جبران کننده هزینه های ناشی از موجودی کالای مازاد نیستند.
چگونه می توان زمان سفارش تا تحویل را کاهش داد ؟
مراحل کاهش زمان سفارش تا تحویل شبیه گام هائی است که در خصوص حذف اتلاف ها برداشته شد.
- گروهی را با هدف کاهش زمان انتظار فعالیت ها از طریق تهیه نقشه جریان ارزش برای فرایند مورد نظر خود در قالب یک تیم تشکیل دهید.
- زمان مورد نیاز فرایندهای دارای ارزش افزوده را محاسبه نمائید.
- نقشه جریان ارزش را مرور کرده و نقاطی را که می توان در آنها زمان سفارش تا تحویل را کاهش داد علامت گذاری نمائید . میتوانید از روش های طوفان مغزی برای برابر نمودن زمان سفارش تا تحویل کل با زمان مورد نیاز برای گام های دارای ارزش افزوده که در قدم قبلی مشخص کرده اید استفاده کنید.
- آن دسته از عواملی که فرآیند شما را تحت فشار قرار میدهند مشخص نموده و برنامه ای برای حذف و یا مدیریت آنها تهیه نمائید به نحوی که اثربخشی فرایند افزایش یابد.
- شاخص هائی را تعریف کنید که قادر باشند مکان و زمان و تکرار فرآیند را مشخص نمایند.
- پس از این که برنامه ای جهت بهبود فرآیند تهیه کردید میزان بهبود را اندازه گیری نمائید.
- این فرایند را برای سایر فعالیت های ناکارای سازمان به کار بگیرید.
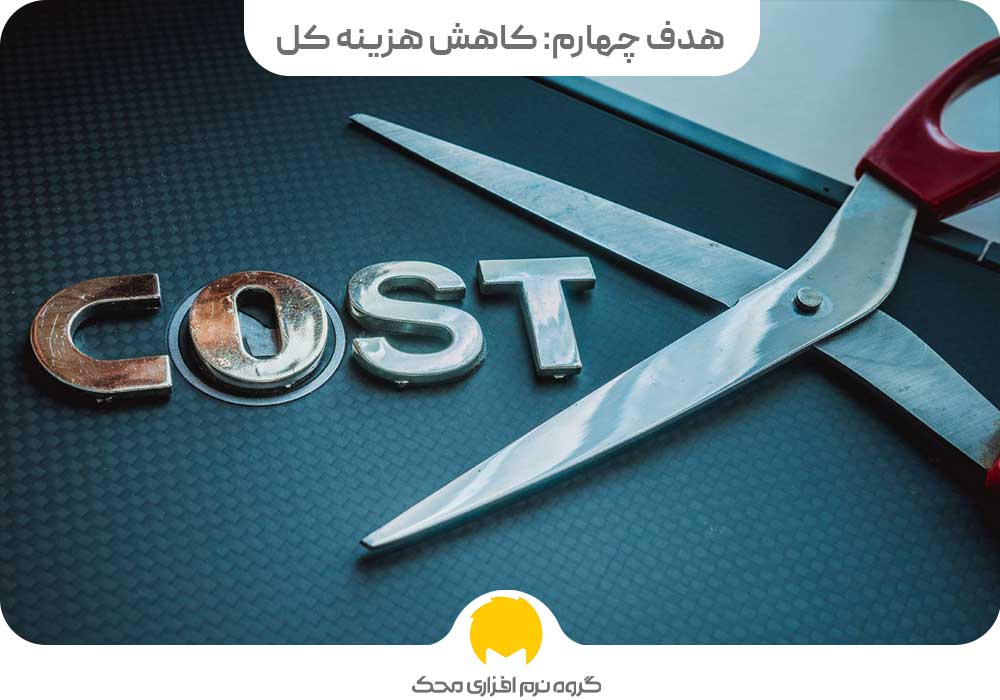
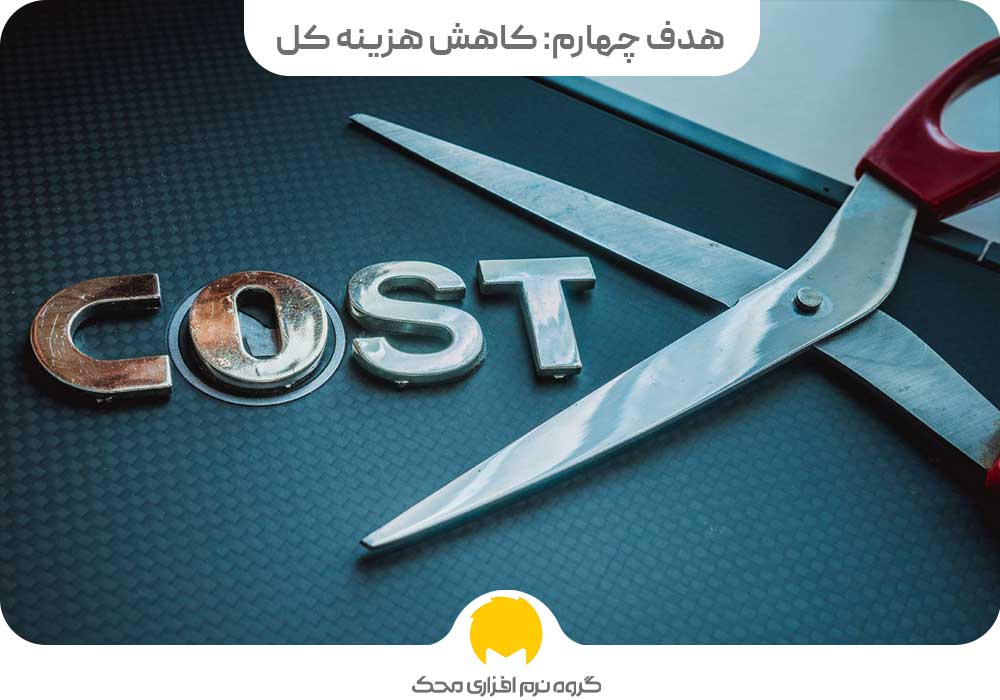
هدف چهارم: کاهش هزینه کل
هزینه کل به صورت مستقیم و غیر مستقیم با تولید کالاها و خدمات مرتبط است. از وظایف سازمان ها ایجاد تعادل بین قیمت کالاها و خدمات با هزینه تولید آنها می باشد. در صورتی که قیمت یا هزینه تولید بیش از میزان معمول رشد کرد شما بازار یا سود خود را از دست خواهید داد. برای کاهش هزینه کل در یک سازمان ناب، اتلاف ها شناسایی و حذف شده و زمان های سیکل فرایند کاهش داده می شوند.
برای کاهش هزینه های عملیاتی در یک سازمان ناب بایستی تنها به تولید اقلامی پرداخته شود که توسط مشتری سفارش داده شده باشند. اشتباه در این است که فکر کنیم تولید بیشتر ،هزینه های تجهیزات تولید (دارایی های ثابت) را سرشکن نموده و از این طریق باعث می شود که هزینه ها کم شوند زیرا این عمل هزینه های انبار و نگهداری کالاها موجب بالارفتن مجموع هزینه های سازمان خواهد شد.
قبل از تعیین فرصت های کاهش هزینه، باید اطلاعات لازم در مورد روش های ردیابی و تخصیص هزینه های سازمان را در اختیار اعضا تیم قرار داد تا در تصمیم گیری ها استفاده شوند. ساختار هزینه ای شرکت ها معمولا شامل دو نوع هزینه های ثابت و متغییر است که در ذیل به طور خلاصه توضیح داده می شود:
هزینه های متغیر: به معنی هزینه انجام کار است. این هزینه ها در صورت تولید یک واحد محصول بیشتر و یا ارائه یک خدمت بیشتر افزایش می یابند. در فعالیت های تولیدی منظور از هزینه های متغیر بیشتر هزینه مواد است.
هزینه های ثابت: هزینه بقا یک شرکت است. این دسته از هزینه ها معمولا شامل هزینه های طراحی تبلیغات و سربار می باشد. هزینه های ثابت با افزایش یا کاهش در تولید و خدمات تغییر نمی کنند.
روش های کاهش هزینه
می توان یکی از روش های ارائه شده زیر را برای تعیین محدوده های مناسب کاهش هزینه در خطوط تولید کالا و خدمات سازمان استفاده نمود. از روش هایی که در ادامه توضیح داده می شوند می توان برای تحلیل و تخصیص هزینه ها در فرآیند طراحی محصول جدید نیز استفاده کرد.
وضعیت رقابتی برای تعیین قیمت کالا یا خدمت جدید: حتما این نکته را به خاطر داشته باشید که قیمت گذاری بر حجم فروش و از این طریق بر میزان تولید موثر است. افزایش و کاهش حجم فروش بر هزینه های ثابت و متغییر محصول اثر دارد و مهم تر این که آیا در چنین شرایطی تولید محصول موردنظر برای شما به صرفه است یا خیر.
تعیین هزینه هدف: قیمت کالا یا خدماتی که در آینده قرار است عرضه شوند از این طریق مشخص شده و میزان سود قابل انتظار را تعیین نماید. هزینه هدف به 3 بخش عمده تقسیم می شود که طراحان را قادر می سازد عوامل هزینه ای را به تولید، خدمت – اجزا و عملیات داخلی و خارجی تفکیک نمایند.
مهندسی ارزش: یک آزمون سیستماتیک عوامل هزینه است که هزینه کیفیت و استانداردهای قابلیت اطمینان را به همراه قیمت محاسبه می نماید. مهندسی ارزش عوامل هزینه را از طریق بررسی بر روی محصولاتی که باید نیاز ها و خواسته های مشتریان را برآورده سازد مطالعه می نماید.
این مطالعه همچنین ارزش های مرتبط با هر وظیفه را در کل عمر محصول یا خدمت تخمین می زند.
تکنیکهای زیر برای تحلیل و بهبود هزینه های عملیاتی سازمان مفید می باشند:
هزینه یابی بر مبنای فعالیت: در این گونه سیستم ها، مخارج مستقیم و غیرمستقیم ابتدا به فعالیت ها و فرایندها تخصیص داده شده و سپس به محصولات، خدمات و مشتریان. برای مثال، ممکن است که سازمان شما بخواهد درصد هزینه هایی که به فعالیت های مهندسی و تهیه مستندات یک گروه از محصولات تعلق گرفته را برای تعیین سود آن محصولات محاسبه نماید. علاوه بر این، می توانید هزینه های غیرمستقیم تخصیص یافته به هر مشتری را هم محاسبه کنید که شما را در انجام تحلیل های مشتری – سودآوری یاری می نماید.
هزینه یابی کایزن (بهبود مستمر): تمرکز این بخش بر کاهش هزینه های صرف شده (خصوصا کاهش اتلافها و زمانها انتظار) در فرایند تولید محصولات و خدماتی است که در حال اجرا هستند.
نظارت بر هزینه: به این معنی که فعالیت های شما تا چه میزان به استانداردهای هزینه که توسط فرایندهای مهندسی یا مالی و براساس هدف گذاری هزینه ای و فعالیتهای کایزن بدست آمده وفادار است.
چگونه می توان هزینه ها را کاهش داد؟
- در ابتدا مشخص کنید که تلاشهای انجام شده مربوط به خط تولید محصولات فعلی است یا خطوط تولید محصولات جدید
- اگر در راستای بهبود هزینه های خطوط تولید محصولات و یا خدمات جدید گام بر می دارید، تکنیک هایی که برای شما مفید است عبارتند از قیمت گذاری هدف، هزینه یابی هدف و مهندسی ارزش.
- در صورتی که هدف بهبود هزینه محصولات فعلی است، محصولات و فرایندهای با بیشترین هزینه را در نظر بگیرید. از روش های هزینه یابی بر مبنای فعالیت، هرینه یابی کایزن و نظارت بر هزینه برای ارزیابی اقدامات انجام شده بهبود هزینه استفاده نمایید.